Większość dystrybutorów robotów współpracujących w kontakcie z Klientami skupia się na niewątpliwych zaletach tych urządzeń. M.in. łatwości programowania i konstrukcji umożliwiającej pracę ramię w ramię z człowiekiem. Jednak od zakupu cobota (który zgodnie z obowiązującymi normami jest maszyną nieukończoną) do stworzenia kompletnej, skutecznej i bezpiecznej aplikacji wiedzie długa droga, na której czeka na nas wiele pułapek.
Rozważasz wdrożenie cobota metodą zrób to sam (z ang. do it yourself, DIY)? Przedstawiamy zagadnienia, które warto uwzględnić przed rozpoczęciem procesu.
Dostępne na rynku roboty współpracujące posiadają tzw. graficzne środowisko programowania. Oznacza to drastyczne ułatwienie programowania cobota w stosunku do klasycznych robotów, gdzie programowanie odbywa się w formie skryptu. Cobot posiada intuicyjne w użyciu funkcje takie jak:
● przejdź do,
● zapamiętaj punkt,
● otwórz chwytak,
● paletyzacja itp.
Są one z pewnością znacznym ułatwieniem w obsłudze robotów.
Nie należy jednak mylić pakietu funkcji programistycznych z algorytmem, jaki będziemy musieli zaprojektować i zaprogramować w celu implementacji budowanej przez nas aplikacji. Algorytm musi przewidywać szereg przypadków i sytuacji, jakie mogą mieć miejsce w trakcie pracy aplikacji. Musi uwzględniać w swojej strukturze wymianę sygnałów z urządzeniami peryferyjnymi (np. obrabiarka CNC, źródło sprężonego powietrza, zasilanie elektryczne). Kolejnym wyzwaniem jest zapewnienie powtarzalnego, stabilnego działania. Oznacza to, że algorytm musi być rozszerzony o szereg warunków/ funkcji sprawdzających. W efekcie powstaje dość skomplikowana struktura (kilkaset linii kodu), gdzie każda nieprzemyślana zmiana może wpływać na skuteczność aplikacji oraz, co ważniejsze, bezpieczeństwo użytkowników. Nietrudno sobie wyobrazić, jak uciążliwa będzie praca z takim algorytmem. Szczególnie kiedy aplikacja będzie wymagała choćby drobnych modyfikacji (np. w związku ze zmianą obsługiwanego asortymentu).
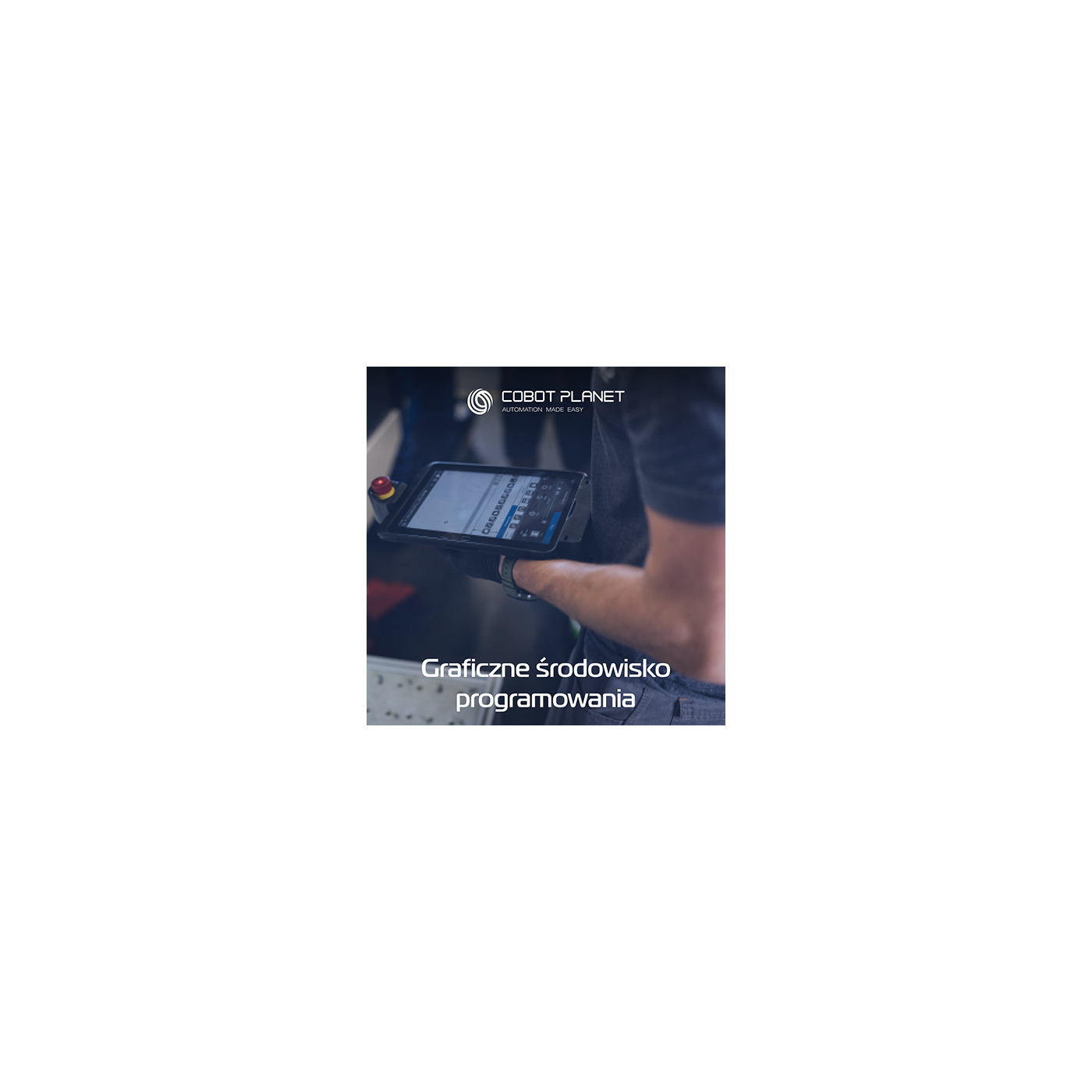
Samo ramię cobota nie zrealizuje oczekiwanej przez nas funkcjonalności. Konieczne jest:
- wybranie narzędzia, które zainstalowane będzie na końcu ramienia (np. chwytak),
- opracowanie sposobu posadowienia cobota, układu elektrycznego do wymiany sygnałów z urządzeniami peryferyjnymi,
- a w przypadku aplikacji machnie tending zaprojektowanie sposobu magazynowania detali, które będą obsługiwane.
Opracowane przez nas rozwiązanie musi spełniać rygorystyczne wymagania Dyrektywy maszynowej. Nawet jeśli podejmiemy się opracowania naszego rozwiązania, wzorując się na dostępnych na rynku urządzeniach i akcesoriach (reverse engineering), musimy liczyć się z wysokimi kosztami wykonania typowymi dla produkcji jednostkowej, kosztami opracowania chociażby szczątkowej dokumentacji, błędami konstrukcyjnymi oraz błędami wykonawczymi. W efekcie uzyskamy rozwiązanie zbliżone do rozwiązania profesjonalnego, ale bez gwarancji, że będzie ono równie funkcjonalne, estetyczne i - co ważne - bezpieczne. Opracowując własne jednostkowe rozwiązanie, ryzykujemy, że nie będzie ono kompatybilne z przyszłymi rozwiązaniami oferowanymi przez producentów (np. współpraca z dedykowanym software).
Kompromisem wydaje się budowanie stanowiska z dostępnych na rynku akcesoriów do automatyzacji. Niezbędne będzie tutaj rozeznanie zalet i wad poszczególnych modułów oraz ich kompatybilności z pozostałymi elementami hardware. Rynek akcesoriów do robotów współpracujących rozwija się. Spotyka się ich coraz więcej, ale są to rozwiania stosunkowo drogie. W dalszym ciągu nie stanowią kompleksowego gotowego rozwiązania.
Obserwujemy rosnącą świadomość przedsiębiorców i kadry kierowniczej w kwestiach związanych z bezpieczeństwem stanowiska pracy oraz troską o warunki pracy personelu.
Podstawowym wymaganiem, jakie muszą spełniać maszyny stosowane w procesie biznesowym jest ich zgodność z wymogami Dyrektywy maszynowej 2006/42/WE. Każda maszyna powinna posiadać deklarację potwierdzająca zgodność z wymogami tej Dyrektywy i być opatrzona znakiem CE. Jest to wymóg bezwarunkowy. Niezależnie od tego, czy urządzenie/maszyna została zakupiona, czy też zbudowana samodzielnie przez przedsiębiorcę tzw. systemem gospodarczym.
Spełnienie wymogów Dyrektywy maszynowej jest kwestią kosztowną. Wymaga znajomości wymogów Dyrektywy, ich uwzględnienia już na wczesnym etapie projektowania rozwiązania, a także przeprowadzenia różnorodnych testów. Te mają potwierdzać osiągniecie wymaganych charakterystyk takich jak:
- elektrostatyczność,
- szczelność,
- zdolność do przenoszenia obciążenia etc.
Komplet wymagań dopełniają niezbędne instrukcje oraz elementy takie jak piktogramy, określające rodzaj stanowiska, czynniki ryzyka oraz wymagane środki ochrony osobistej.
Kiedy potwierdzimy, że zbudowana przez nas aplikacja spełnia wymogi Dyrektywy maszynowej możemy przystąpić do kolejnego etapu jakim jest ocena ryzyka. Ta powinna być przeprowadzana każdorazowo po instalacji urządzenia i przed oddaniem go do użytkowania. Audytor (specjalista z dziedziny bezpieczeństwa pracy) określi, czy stanowisko spełnia wymogi bezpieczeństwa. W wyniku audytu określone zostaną obszary ryzyka wymagające korekty przed włączeniem stanowiska do użytkowania oraz takie, które należy skorygować, ale już w trakcie eksploatacji maszyny.
Ocena ryzyka jest procesem niezależnym od procesu uzyskania znaku CE i jest wymagana w świetle obowiązujących przepisów prawa. Warto w tym zakresie nawiązać współpracę z niezależnym ekspertem. Opracowując aplikację bez rozpoznania wymogów Dyrektywy maszynowej, musimy liczyć się możliwością ujawnienia krytycznych uchybień na etapie oceny ryzyka. Może się to wiązać z koniecznością wprowadzenia kosztowych modyfikacji i opóźni oddanie stanowiska do eksploatacji.
Trudno sobie wyobrazić kompletną aplikację, w której cobot nie współpracuje z innymi urządzeniami. Szafki sterowania robota wyposażone są w moduły I/O, obsługujące podstawowe formuły i protokoły komunikacji (sygnały cyfrowe, analogowe, RS, modbus itp.) Często okazuje się, że liczba dostępnych I/O jest niewystarczająca dla naszej aplikacji. Lub że producent cobota nie przewidział miejsca na zainstalowanie dodatkowych sterowników i hardware, umożliwiających korzystanie z Ethernetu, control boxów wymaganych przez niektóre modele chwytaków, przekaźników separujących układy elektryczne cobota i urządzenia peryferyjnego. Braki mogą dotyczyć również rozwiązania tak prozaicznej kwestii, jak umieszczenie nadmiarowego odcinka przewodu łączącego szafkę sterowania cobota z jego ramieniem.
Sprawa komplikuje się dodatkowo, kiedy chcemy, żeby nasze stanowisko miało charakter mobilny. Tzn. kiedy planujemy przenoszenie stanowiska i podpinanie różnych urządzeń peryferyjnych w zależności od potrzeb. Chodzi np. o przenoszenie stanowiska pomiędzy maszynami CNC. Bez odpowiednich rozwiązań po stronie wymiany sygnałów przeniesienie stanowiska wiąże się każdorazowo z ingerencją w szafkę sterowania robota i ręczne podpinanie przewodów. Jest to przede wszystkim niewygodne, a także naraża elektronikę cobota na uszkodzenia. Wymaga od personelu stosownych kwalifikacji i uprawnień.
Przewidywana skala wdrożeń uzasadnia ponoszenie wysokich kosztów oraz zaangażowanie interdyscyplinarnych zespołów (programowanie, projektowaniem, automatyka, BHP) w pracę nad oferowanym rozwiązaniem. Mowa tu o znaczących budżetach i nakładach kompletnie nieuzasadnionych z punktu widzenia jednostkowego wdrożenia. To ten aspekt sprawia, że profesjonalni producenci mogą oferować zaawansowane i dopracowane rozwiązanie po atrakcyjnych cenach. Długofalowe podejście pozwala na udoskonalanie rozwiązania na podstawie informacji zwrotnych od użytkowników.
Przykładem jest tu warstwa oprogramowania, gdzie producenci stale rozszerzają oferowaną funkcjonalność. Aktualizują swoje oprogramowanie do najnowszych wersji systemów operacyjnych cobotów, dbając jednocześnie o kompatybilność programistyczną rozwiązań.
Przedsiębiorcy są świadomi, że dysponują ograniczonymi zasobami finansowymi, materialnymi i kadrowymi. Codziennie podejmują decyzje o angażowaniu tych zasobów w sposób optymalny dla swoich firm. Często te decyzje sprowadzają się do wyboru między realizacją projektu A (projekt lepszy) kosztem projektu B (projekt dobry).
Nie inaczej jest z kwestią wdrożenia cobotów. Dylematem jest:
● czy w tym procesie skorzystać z doświadczeń profesjonalnych firm, uzyskać dostęp do ich know-how, a tym samym osiągnąć zakładane korzyści w krótkim i przewidywalnym horyzoncie czasowym oraz pozwolić własnemu personelowi skupić się na core biznesie
● czy też wejść na ścieżkę, która potencjalnie da nam dużo satysfakcji, ale jednocześnie każe nam się zmierzyć z wieloma nieprzewidywalnymi problemami, może okazać się znacznie bardziej kosztowna niż zakładaliśmy. Może wymagać od nas kompetencji, których nie potrzebujemy w bieżącej działalności oraz wiązać się z braniem na siebie ryzyka, którego nie jesteśmy w ogóle świadomi, nie mówiąc już o byciu przygotowanym.
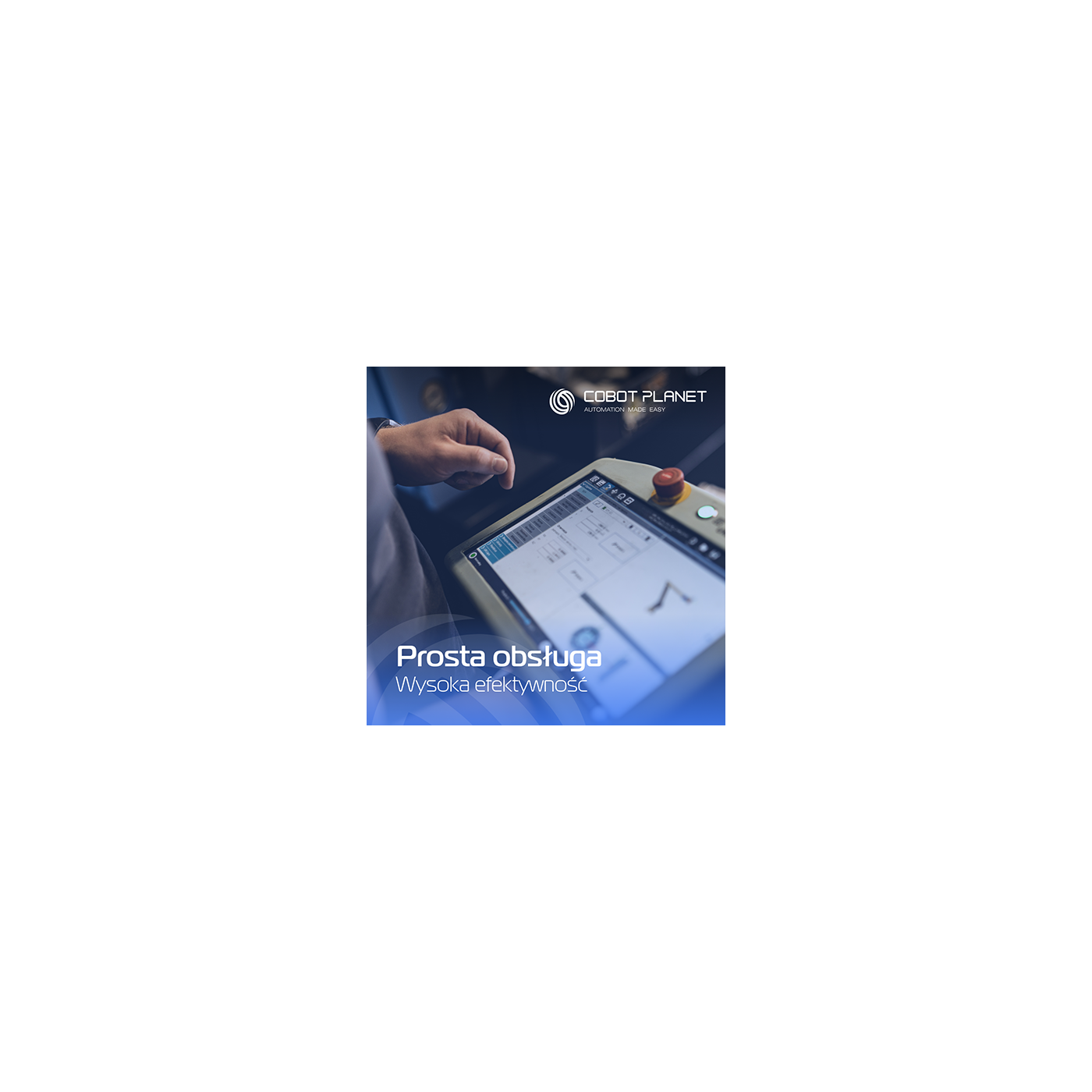
Zdecydowana większość przedsiębiorców i menadżerów wie, że automatyzacja jest nieuchronna. Mamy nadzieję, że przekazane informacje będą dla Państwa przydatne przy podejmowaniu ważkich decyzji biznesowych. Zespół Cobot Planet chce dzielić się z Państwem swoją wiedzą oraz doświadczeniem. Pozostajemy do Państwa dyspozycji i zachęcamy do kontaktu z naszymi ekspertami. Chętnie odpowiemy na pytania związane z wdrożeniem cobota w Państwa firmie.